Reliable Quality Management System is critical to long term Outsourcing Projects. We have personnel with following qualifications & experience.
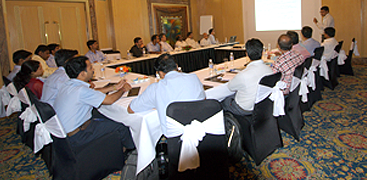
- ISO 9000 Lead Auditors.
- Metallurgists with Quality Management experience in Steel Casting, Forging, Steel making, Fabrication processes, Gear & Engine Machining & Inspection.
- ASNT Level III & II qualified NDE staff, including Radiography, Ultrasonic, Magnetic Particle, Die Penetrant Testing.
- International exposure in Approval Processes of critical Customers & Industry Institutions like Aramco, BP, Exxon Mobil, Shell, Total, Petrobras, Norsok, Vestas, CE-PED, Water Boards, and other similar approvals.
- We have qualified & experienced Welding Engineers and we are familiar with Pressure Vessels Codes ASME Sec IX, Norsok, ABS & DNV Drilling and Offshore Classifications. We have qualified Inconel 625 Cladding over 4130 & F22.
- Experienced in working with Customer designed Material Specifications or designing Material Specifications based on given application requirements.
We follow following processes to ensure that Quality Management Systems are delivered agreed Quality parts and certification.
Factory Audits:
- We Audit all New Vendor's manufacturing locations, where Quality Systems, Manufacturing Processes, Personnel qualification and HSE are critically reviewed. Our Audits are spanning entire Supply Chain, primary manufacturing (Steel Mill), Forge or Foundry, Machining, Surface Coating and assembly, so as to gain control and visibility of processes and its compliance, with Vendor QMS, Industry Standards & Customer standards.
- We have several audited and approved Third Party Independent NABL accredited Test Labs for Customer specific requirements. These are important for Testing Qualification Samples, instead of sending this abroad to Customer location Or to test them at Vendor facility.
- We have continuous Audit plans where Existing Suppliers are subjected to Audits to ensure continued compliance.
Source Inspection:
- We carry out Sample, Pilot and on-going Source Inspection, and Customers Quality and Certification requirements are strictly enforced. Our Inspection & Audit Report are sent directly to Customers Quality teams, so that your requests are directly implemented on factory floors.
- Our Inspection processes including packing and certification.
- Our Inspection and Control processes are so well established that for several Customers we can arrange Drop-Ship parts to End Customer, where the consignment is shipped to a third country or Project site.
- Our present approved supplier base has 90% or more shipments being despatched with Vendor’s self-certification with 99,8 % Quality Performance Scores. Our ultimate aim is to create robust Manufacturing and Inspection processes at Vendors location, so that customer need not spend on source Inspection.
Surveillance Audits and Random samples :
- Existing approved Vendors have to undergo, continuous and rigorous oversight by way of Surveillance Audits, to maintain Quality levels established during Vendor Qualification stage. These Audits are surprise Audits carried out based on risk assessment due to Value and Volume spent, NCR Trends and criticality of Products.
- We also pick up Random samples from bulk Production, during Vendor visits, without informing in advance. These are tested at Third Party Laboraory to Qualification standards & results are critically reviewed. We ensure Vendor takes immediate corrective actions if there are serious concerns observed during Audit & Random Sample Tests. Vendor needs to demonstrate that all quality issues are resolved.
Quality Reporting & travel at Customer Plant locations:
- Our Quality team reviews & records supplier Quality Performance on agreed KPIs. The Quality Scores are regularly monitored, and shared with Customers.
- We aim is to provide transparent and responsive Quality Organisation that is synchronized with Customer’s internal Quality systems and procedures.
- To understand and get first-hand information of applications at Customers end, we travel frequently and work shoulder to shoulder with Customers Quality and operations teams. This includes travel to Offshore Locations at North Sea, meeting Customer’s end Customer & visiting Wind Mill sites and SubSea vessels.